Overhead Crane Accidents & Safety Measures
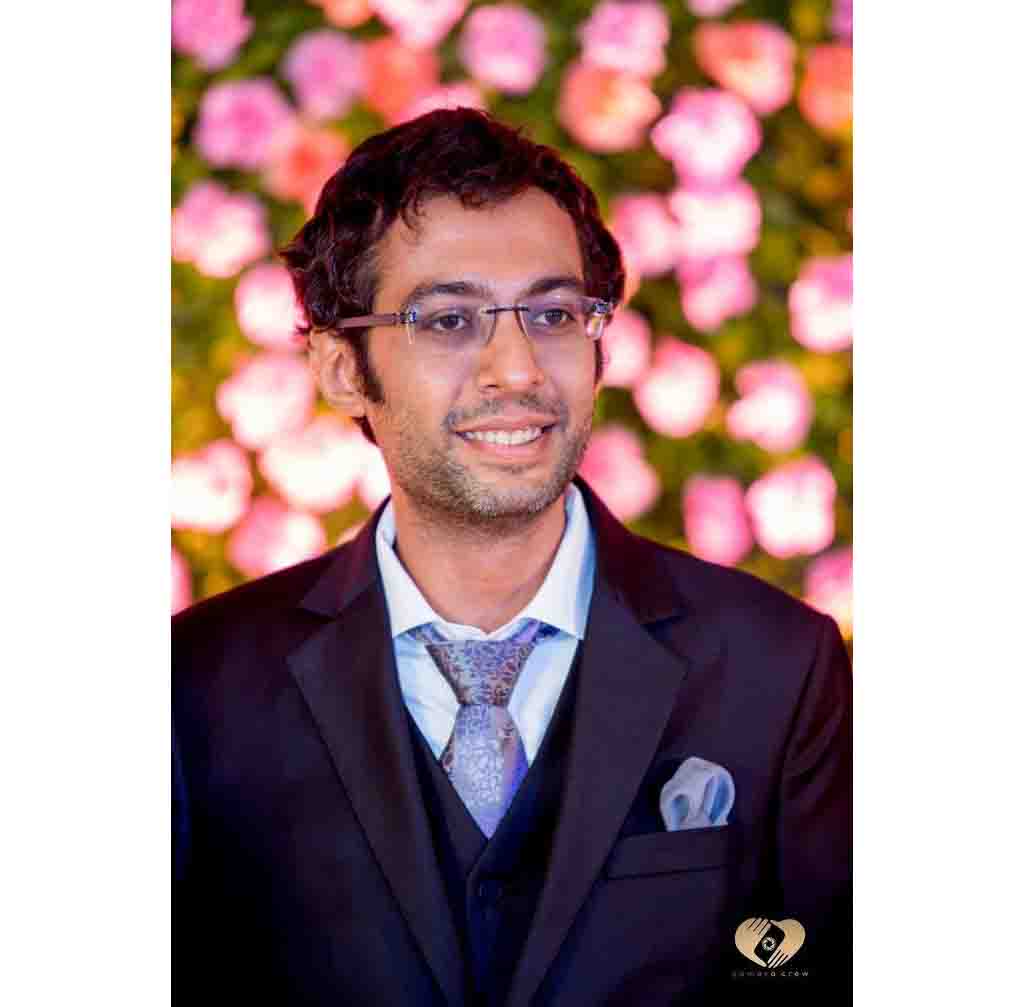
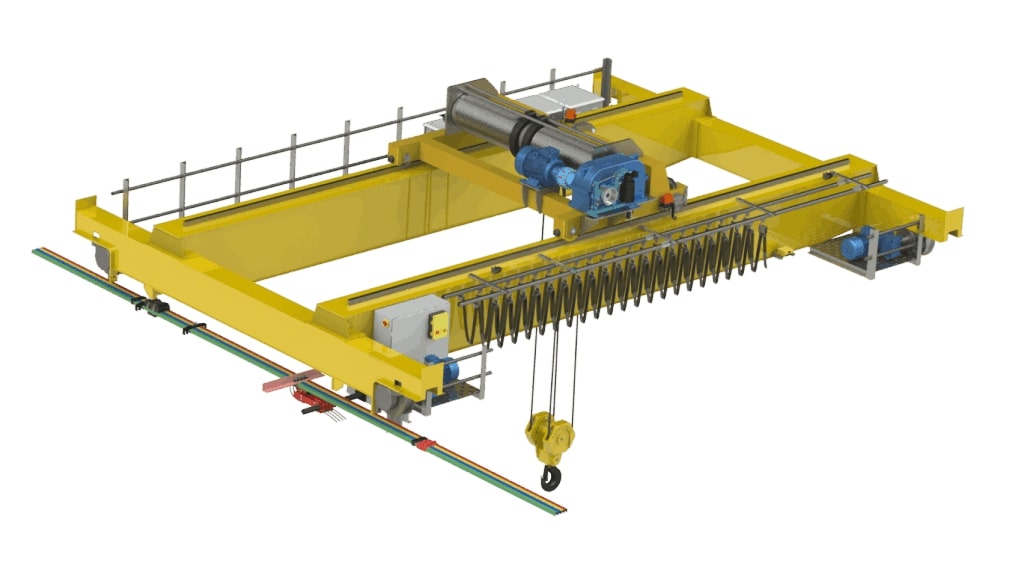
Cranes have been used to ease human labour since 3000 BC, remaining– for the most part – inconspicuous workhorses. The first ever crane was called the Shadouf and used a lever mechanism to lift water for irrigation. The machine was invented Iraq (Mesopotamia) and later used in Egypt [1,2,3,4]. Over the centuries, cranes gradually evolved assuming new forms, structures, and mechanisms, until today there exist different types of cranes having varied uses and applications.
Types of Cranes :
Cranes may be classified in many ways, such as the industries that use them, the mechanism involved, the portability and certain other factors. In general, cranes may be classified as mobile cranes and overhead cranes with many sub-categories under each classification. Overhead cranes may be any of the following types depending upon the component parts and the mechanism used [18,19].
- Bridge Cranes
- Gantry Cranes
- Monorail Cranes
- Jib Cranes
- Workstation Cranes
There are a number of sub classifications within each classification. For example, bridge cranes or gantry cranes may be further classified as single or double girder depending on whether a single or double cross girder is used. Naturally, the crane capacity for double girder is higher than that of a single girder crane. There is no universally accepted standard classification of cranes. However, the categories mentioned here will suffice for the purpose of this guide to safety of overheard cranes.
Who needs overhead cranes? :
Overhead cranes a.k.a. bridge cranes are used to transport heavy material over a long distance. Bridge cranes cover significantly longer distances as compared to tower cranes or mobile cranes.Overhead cranes may be used to move products along an assembly line, load finished goods for transportation, transfer components for further processing, or transporting heavy goods for storage. Industries that typically use overhead cranes include the automotive industry, manufacturing industry, the steel industry, the warehousing industry, the steel industry, and the construction industry [20]. Applications typically include loading or unloading of ships, transporting heavy material at construction sites, and transporting component parts along an assembly line. Depending on the site, application, and distance traversed, a single girder, double girder, JIB, or other type of overhead crane may be used.
Need for Safety:
Three important considerations for designing cranes that remained unchanged through
the centuries were – the crane must be capable of lifting heavy load, the crane must not tip when lifting the load, and the crane parts
must not be damaged during operations. Another important consideration – particularly during operation of cranes – is that no human must
be harmed during the operation of cranes.
OSHA[21] records show that more than half of the crane accidents are a direct result of inadvertent contact with a power source.
A metal part of the crane brushes against a power source causing electrocution of the crane, bodily harm to the operator,
and harm to those within the range of current. Of the recorded deaths, most are crane operators. Further investigation reveals
that improper safety planning, insufficient preventive safety measures, and insufficient operator training led to these accidents.
Material overload is the second most significant cause of overhead crane accidents. According to OSHA, 80% crane accidents occur
as a direct result of overload causing irreparable damage to the crane and harm to the operator as well as other onsite personnel.
Statistics show that one accident of overload occurs for every 10,000 work hours.
Machine failure, slipping, and two blocking are other causes of crane accidents. About 20 deaths occurred as a direct result of
accidental material drop in the year 2012 alone.
Most crane accidents occur due to oversight and lack of forewarning – two factors which are easily remedied. We now examine crane
accidents in further detail.
How frequently do accidents occur? :
Crane accidents are not unique to contemporary cranes. In the year 2006 for instance, there were 72 fatal crane related injuries. Between 2003 and 2005, the number of accidents averaged 78 every year. This includes both fatalities that can be directly attributed to crane operations as well as secondary fatalities. Majority of these incidents were related to mobile, rail, and overhead cranes [6]. The above-mentioned fatalities included labourers, electricians, welders, cutters, solderers, and brazers – ergo ground personnel were equally affected, as were operators. Industry related statistics show that fatalities in manufacturing were far more than those in mining. The most number of accidents occurred in Texas followed by Florida, California, and Louisiana [7]. More recently, in the USA the following are the statistics for the states having the maximum number of crane related fatalities -
State of the incident | Number of fatal injuries involving cranes |
Texas | 40 |
Illinois | 12 |
Florida | 11 |
California | 10 |
Pennsylvania | 10 |
Very little statistics relating to crane specific incidents are available with respect to India. What little information is available is with respect to compensation paid to those affected [17] The situation is indeed grim but it can be rectified. First however, a word on what causes crane accidents.
Causes of Crane Accidents :
Typically, a crane has a hook and line system mounted on a beam. The beam in overhead cranes runs on parallel rails. Mobile cranes are mounted on trucks or rails whereas EOT cranes are stationery [6]. Ground personnel guide a crane operator during operations. There are three important areas of risk during any crane operation – unintentional contact of metal parts with electric power source, accidental drop of material, and overload. Failure or malfunctioning of one or more parts may also result in a mishap. Other areas of risk include errors in judgement by the operator, or miscommunication between operator and ground staff. OSHA (Occupational Safety and Health Administration) identifies the following proximate causes[5] for crane accidents –
- Bridge Cranes
- Gantry Cranes
- Monorail Cranes
- Jib Cranes
- Workstation Cranes
While these are the proximate causes of crane accidents, these accidents may occur due to any or all of the following conditions –
- Instability of the crane
- Instability of the load
- Faulty parts
- Proximity to electric power source
- Proximity of ground personnel to crane operation area
- Communication gap between ground personnel and crane operator
- Training gaps
- Maintenance gaps
All of this boils down to improper monitoring of the conditions or environment surrounding the crane operation – particularly with respect to maintenance of crane and crane parts, proximity of metal parts to power source, failure to replace faulty or malfunctioning parts in a timely manner, and miscommunication between ground personnel and operator. Moreover, if the ground personnel are standing too close to the crane, they too are at risk as evidenced by the statistics below.A close monitoring of the crane and its operation can help reduce – and even completely mitigate – the risk of accident.
Guidelines to prevent crane accidents:
OSHA has examined a myriad of overhead crane accidents and identified the precautions to be taken to prevent them [9] -
- Inspection of the machine by a qualified inspector before every operation to check for any mechanical faults
- Regular comprehensive inspection to pre-determine any faulty wiring, damaged parts, or frayed ropes or coils
- Repairs by a qualified and trained person
- Operation by a trained person who understands the rigging and the balance points for load.
- Chock the load whenever possible
- Avoid working under suspended loads
- Periodically review the load capacity and safety margin of the equipment
- Use the equipment at slightly below capacity
- Mark out a danger zone – suggested 90 feet radius – and do not work within this zone.
- Draw up a pre-work plan identifying hazards, event sequence, and danger zones
- Identify pinch points
- Identify and follow removal procedures
Apart from the physical precautions such as marking out the danger zone, these guidelines repeatedly, highlight three precautionary measures –
- 1. Identify risk in advance of operation
- 2. This may be done by periodic scheduled inspections and inspection before every operation
- 3. Regular maintenance of the cranes
In India the provisions of the Bureau of Indian Standards (BIS) Act (1986) has published a legal document that details the norms for manufacture, erection, operation and maintenance of cranes and crane parts [16].
Crane Inspection and Maintenance Protocol
OSHA [11] as well as the BIS [16] recommends that all active cranes should be inspected at least once a year in order to identify potential problems. A trained inspector having a minimum experience of 2000 field hours dealing with servicing and maintenance of cranes should conduct inspection of cranes says CMAA (Crane Manufacturers Association of America). ANSI recommends four categories of inspection –
- Initial – prior to first use (OSHA 1910.179). Overhead cranes must also undergo a rated load test – according to ANSI B30.11. The actual load should not be more than 80% of that tested.
- Functional – The functionality of the crane must be tested before every shift. Specifically, maladjustments, leak in tanks, valves, pumps and other parts, chains and ropes, hooks, and other components must be checked for wear.
- Frequent – Frequent inspections must be conducted based on the usage of the crane. Thus, a heavy service crane may be inspected weekly. During these inspections, particular attention must be paid to load chain, wire rope, and hoist brake. The inspector must listen for abnormal sounds.
- Periodic inspections may be conducted annually or with greater frequency depending on the usage. Attention must be paid to all operational parts of the crane for wear and potential malfunctioning.
Extending the Crane Work Life
If the crane is new, it is perhaps built as per regulatory standards and requires
little care. However, if you are using an older crane, or plan to use your new crane as heavy service equipment, it is important to
understand the work life of a crane [13,14,15], and how you can get the maximum productivity from your crane at the lowest cost.
A crane has many components that may deteriorate, malfunction, or simply break down – requiring costly maintenance and downtime.
Understanding the causes of breakdown is important if you wish to get the maximum productivity out of your crane.
The two major factors that cause deterioration in cranes are corrosion and fatigue. Corrosion is the result of environmental factors
while fatigue is caused by varying loads and extensive use over long periods. Both factors are controllable with proper care and maintenance.
Corrosion is easily controlled through plating techniques that protect the surface layer of component parts. Managing fatigue however is
a challenge.
Any steel structure has some built in cracks that react to stress. Depending on the force and frequency of stress, these cracks widen
causing component parts to malfunction. In cranes, the force of stress varies with the load. The more the fluctuations in the weight
of the load – and consequently the stress – the faster the cracks will widen. Cracks grow faster on thicker components as compared
to thinner ones. Soldered connections tend to crack faster than bolted joints. In overhead cranes, the wire ropes or coils used may
succumb sooner because of fluctuating tension. Tension may also be caused due to frequent braking and reversing.
Frequent and untimely breakdown may be avoided by mapping the usage and identifying faults early, thus facilitating planned downtime.
This, coupled with periodic maintenance as well as timely replacement of cranes and crane parts can not only ensure safety in crane
operations but also save your business extensive costs in terms of loss due to down time and healthcare compensation.
The Cost Factor
Inspection and maintenance costs depend on several factors [12] including the type of crane, the number of component parts, the time taken for inspection, the frequency of inspection, the number of parts to be repaired or replaced, and the extent of damage or wear and tear. Natural wear and frequency of inspection will in turn depend on usage – both with respect to time as well as load. Some other factors that may affect the cost of inspection include whether the inspector will carry his own testing equipment and the time the inspector spends in travelling to the site. The inspector’s level of experience may also affect the cost. Besides the cost of the inspection itself, there may be some additional and hidden costs such as cost of down time and cost of repairs and replacements. These costs can be minimized by predictive maintenance practices and a little bit of caution.
Introducing CraneSCADA – The crane monitoring and predictive maintenance system
The recent wave of digitization has driven a new change – Industry 4.0 –,
which has touched everything from procurement to manufacturing and marketing. It has also touched the industries associated with
– and using – cranes. IoT (Internet of Things), AI (Artificial Intelligence), and ML (Machine Learning) are being leveraged to
make the work of humans easier – and safer. In fact, Industry 4.0 is nothing but a concept that envisions connected machines
and humans all working in tandem towards the fulfilment of one goal – satisfying the consumer.
CraneSCADA has made one such effort towards safety in crane operations.
CraneSCADA (Crane Supervision, Control And Data Acquisition) is an IoT platform for industrial cranes that enables remote supervision,
monitoring, and control of cranes and helps predict and prevent crane accidents.
As discussed above, most crane incidents are a result of missing subtle signs of wear, improper training, and oversight.
Moreover, a good deal of time and money is spent on repair and maintenance resulting in costly downtime and wasted expenses.
This waste can be greatly reduced if the problem is sighted well ahead of time and corrective action is taken in a timely and planned
manner. CraneSCADA enables such predictive maintenance and proactive intervention with its IoT enabled crane maintenance application.
Email us at info@cranescada.com if you want to get in touch
References:
- Paipetis, S. A.; Ceccarelli, Marco (2010). The Genius of Archimedes -- 23 Centuries of Influence on Mathematics, Science and Engineering: Proceedings of an International Conference held at Syracuse, Italy, June 8-10, 2010. Springer Science & Business Media. p. 416. ISBN 9789048190911.
- Chondros, Thomas G. (1 November 2010). "Archimedes life works and machines". Mechanism and Machine Theory. 45 (11): 1766–1775. doi:10.1016/j.mechmachtheory.2010.05.009. ISSN 0094-114X.
- Sayed, Osama Sayed Osman; Attalemanan, Abusamra Awad (19 October 2016). "THE STRUCTURAL PERFORMANCE OF TOWER CRANES USING COMPUTER PROGRAM SAP2000-v18". Sudan University of Science and Technology. The earliest recorded version or concept of a crane was called a Shaduf and used over 4,000 years by the Egyptians to transport water.
- Faiella, Graham (2006). The Technology of Mesopotamia. The Rosen Publishing Group. p. 27. ISBN 9781404205604.
- https://www.graphicproducts.com/articles/crane-accidents/
- https://www.bls.gov/iif/oshwc/osh/os/osh_crane_2006.pdf
- https://www.bls.gov/iif/oshwc/cfoi/cranes_fact_sheet.htm
- https://www.osha.gov/dts/maritime/sltc/ships/rigging/rigging_accidents.html
- https://cranerepairco.com/blog/crane-inspections-often/
- https://www.mazzellacompanies.com/resources/blog/how-much-does-an-overhead-crane-inspection-cost
- https://www.usbr.gov/research/projects/download_product.cfm?id=1543
- https://ideascranes.com.au/how-to-maximise-crane-asset-life/
- https://law.resource.org/pub/in/bis/manifest.med.14.html
- https://en.wikipedia.org/wiki/crane_(machine)#types
- http://www.mhi.org/fundamentals/cranes