EOT Cranes - Electric Overhead Travelling Cranes.
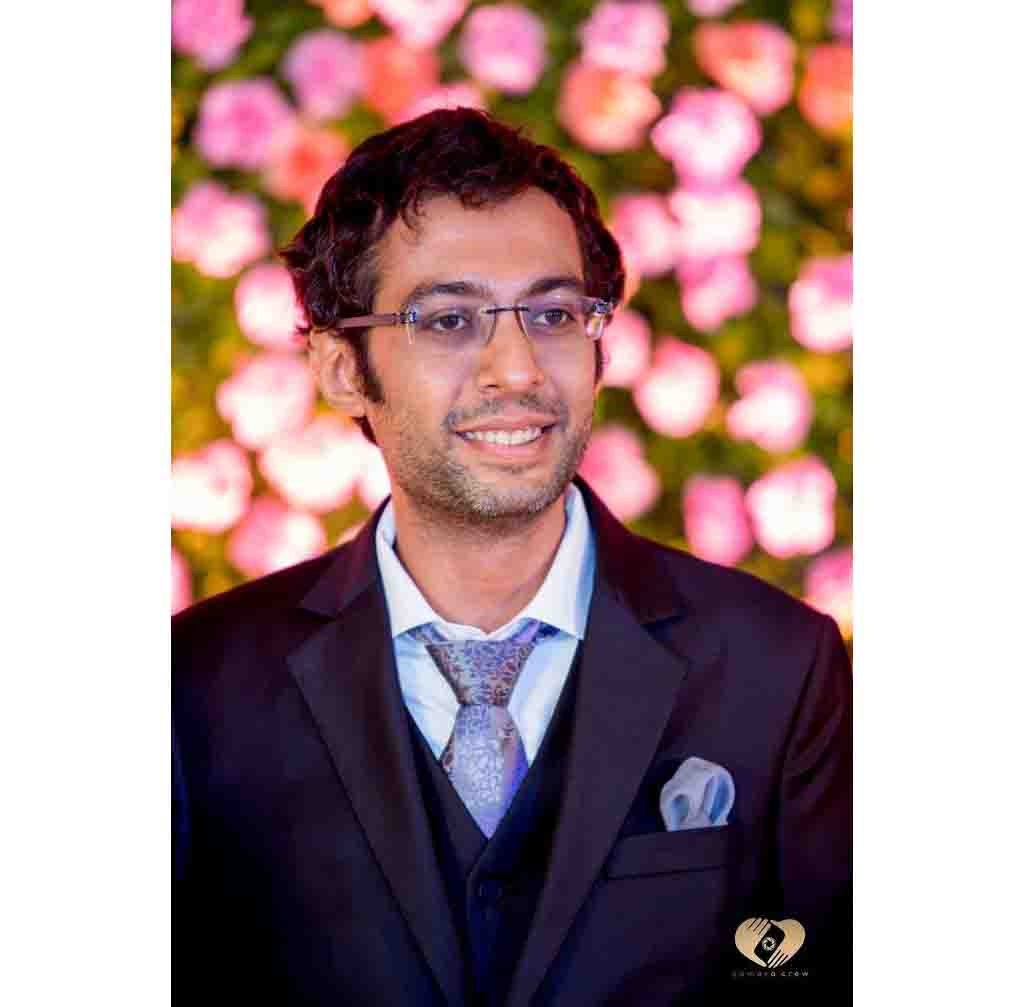
In todays Blog we will discover what are
EOT Cranes.
Where are they used? What are the different types of EOT Cranes?
So if you want to make sure that your knowledge of the EOT Cranes
is up to speed, you should get a lot of value from today’s content.
- EOT (Electric Overhead Traveling) Crane Configurations
- Parts of EOT Cranes
- Features of EOT Cranes
- Types of EOT Cranes
- Applications of EOT Cranes
- Malfunctions of EOT Cranes
- Comparison of EOT Cranes with Other Types of Cranes
- Conclusion
Introduction
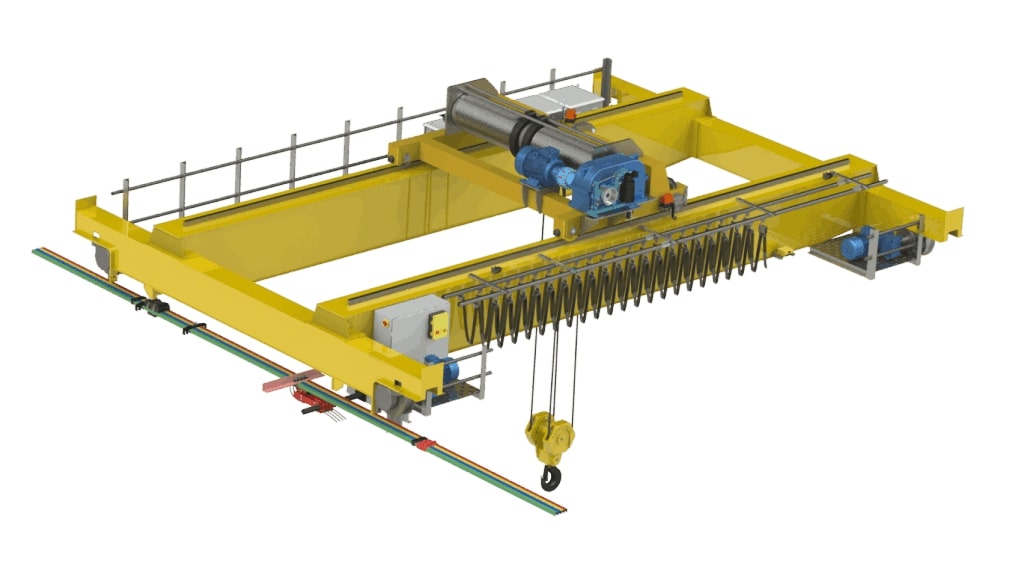
In 1876, Sampson Moore in England was the first Manufacturer of Electric Overhead Crane.
Moving a heavy or bulk load from one place to another crane mechanism is used, which reduces the manpower
and provides high productivity and efficient work.
EOT (Electric Overhead Traveling) crane is one of the types of overhead cranes, which is also called as
bridge cranes.
EOT cranes operate on electricity. It needs an operator or pendant station to control the functions of
the EOT crane.
It consists of a parallel runway connected with a traveling bridge. The hoist is mounted on a traveling
bridge. It is used for critical industrial applications.
An EOT has three working movements: Crane Hook Up and Down Lifting, Trolley Lateral Movement, and Crane
Long Traveling Longitudinal Motion
Watch our video for understanding Thruster Brakes for EOT cranes.
EOT (Electric Overhead Traveling) Crane Configurations
-
Under Running EOT Cranes
EOT cranes that are supported by the roof structure and run on the bottom flange of runway girders are known as under-running EOT cranes. These cranes have a small trolley dimension which allows them to utilize the maximum building width and height. Additionally, the under-running configuration allows for the use of existing ceiling girders for protecting the crane track. This configuration is best suited for applications where the crane must be installed in an existing building and space is limited. One of the major benefits of under-running EOT cranes is that they allow for a more efficient use of the available space in a facility. They also tend to be more cost-effective than top-running cranes since they do not require the installation of new runway beams. However, they do have a lower capacity range than top-running cranes, which limits their ability to handle heavy loads. -
Top Running EOT Cranes
EOT cranes that have a fixed rail or track system installed on the top of the runway beam are known as top-running EOT cranes. The top-running configuration does not have any limiting capacity range and can handle both small and huge loads. This configuration is best suited for new construction projects or for applications where the crane must be installed in a new building with a high headroom. One of the major benefits of top-running EOT cranes is that they have a higher capacity range than under-running cranes, making them more versatile and able to handle heavy loads. They also tend to be more durable and have a longer lifespan. However, they are generally more expensive to install since they require the installation of new runway beams, and also take up more space in a facility.
Overall, the choice between under-running and top-running EOT cranes depends on the specific application and the available space. Under-running EOT cranes are ideal for retrofit projects where space is limited and existing ceiling girders can be used for protecting the crane track. On the other hand, top-running EOT cranes are ideal for new construction projects or for applications where high headroom is required. It is important to note that both types of EOT cranes have their own advantages and disadvantages and careful consideration should be given to the specific needs of the application before making a final decision.
Parts of EOT Cranes
An EOT crane is made up of several key components, including the hoist, trolley, bridge, columns, runway, end effectors, reinforced-steel cable, hook, master controllers, electrical control panel, DSL busbars, radio remote control, and pendant.
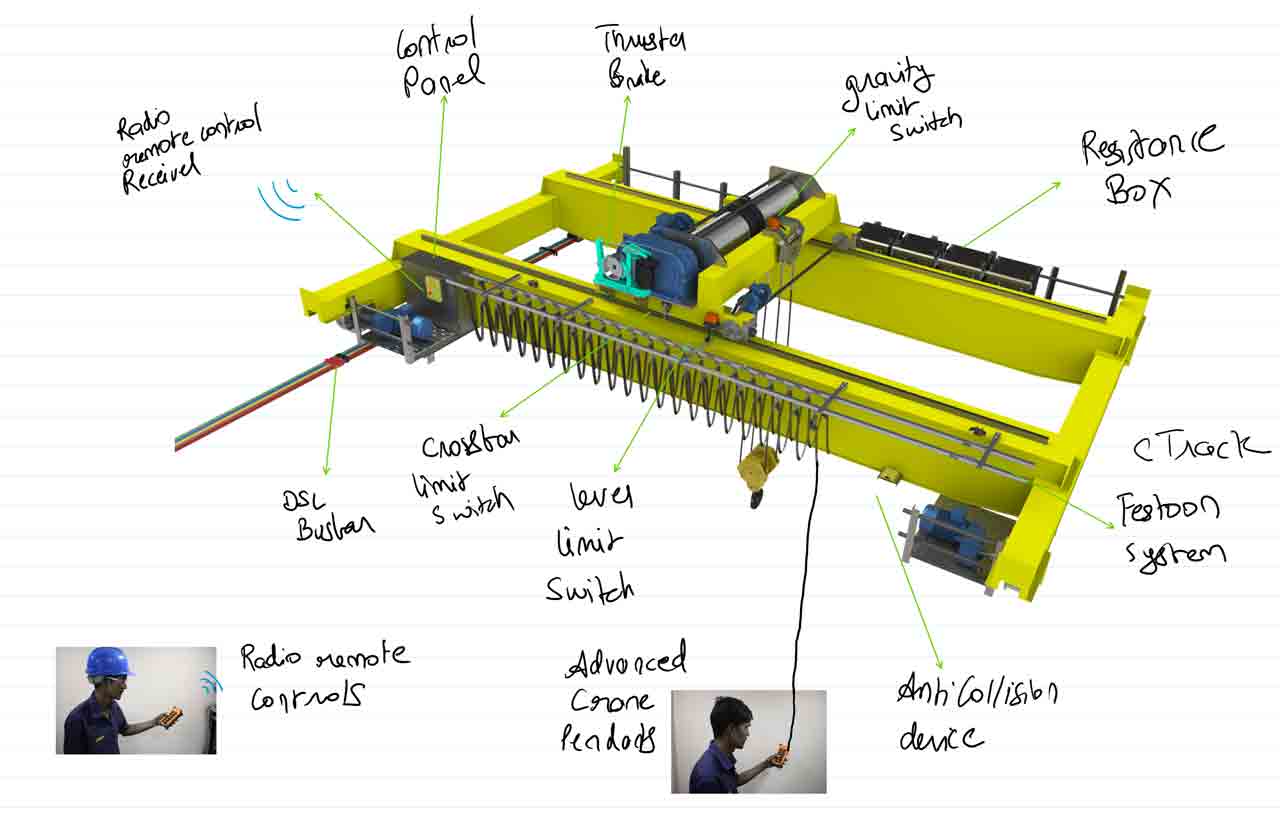
-
Hoist
- The hoist is what creates the lift in lifting systems by holding, raising, or lowering the load using wire rope or chains.It is the most important component of the crane, and it must be able to handle the maximum weight of the load.
-
Trolley
- Trolley’s support the hoist and moves along the crane’s bridge. Trolleys can be configured to be top-running or bottom-running and can be within a track system or run on a beam.The trolley is responsible for moving the load horizontally.
-
Bridge
- It’s a primary structural component of a lift that connects the runways and holds the hoists and trolleys, also a load-bearing component that runs the width of the crane system.
-
Columns
- If the crane support system isn’t part of the building it will need columns to support it. How high your columns are will determine your headroom and how high your lift can go.
-
Runway
- Runways are what the bridge travels along and move the crane up and down the bays.
-
End Effectors
- End effectors are the “grab” part of the crane system.They are responsible for gripping and releasing the load.
-
Reinforced-steel cable
- Reinforced-steel cable lines run from a winch just behind the operator's cab, extending up and over the boom and jib.
-
Hook
- The load is supported using a hook that connects to the hoist and to the end effector.
-
Master Controllers
- There are two master Controllers in the cab. One controls the left-to-right movement of the boom, and the other controls forward and backward movement.
-
Electrical Control Panel
- Control Panel of EOT Crane is a steel box containing all the motor driving equipment such as VFDs , contactors , fuses , switches & all connections to limit switches.This is the heart of the crane control system and is responsible for controlling all the electrical functions of the crane.
-
DSL Busbars
- Busbars are made up of highly electrically conductive metals and they distribute & carry power from a source to a destination or multiple destinations.They are used in EOT Cranes to supply power from the grid to the crane control panel.
-
Watch our video for understanding MAKS Crane Remote Control.
Radio Remote Control
- Radio remote controls wirelessly control EOT Cranes from a safe distance.This allows the operator to control the crane from a remote location, such as the ground or a nearby control room.
-
Pendant
- Pendant controls are wired control of an EOT crane.They are connected to the crane control system by a cable and allow the operator to control the crane.
Motions of an EOT Crane
- the EOT Crane can move in 3 directions with the help of electric Motors-
-
Hoisting Travel:
- Hoisting Motion Travel is used to take the hoist up and down.
-
Cross Travel:
- Cross travel is used to take the hoist left or right.
-
Long Travel:
- Long travel is used to take the crane forward or backward.
Features of EOT Cranes
EOT Cranes are designed to be highly efficient and safe, and they have several features that make them ideal for industrial applications. High Efficiency - EOT Cranes are highly efficient and can handle heavy loads with ease. They use advanced technology such as VFDs and advanced control systems to ensure that the crane is operating at its maximum efficiency at all times. Safety - EOT Cranes have many safety features such as emergency stop buttons, limit switches, and overload protection to ensure the safety of the operator and the load. They also have built-in safety features such as anti-collision systems to prevent accidents. Easy Maintenance - EOT Cranes are easy to maintain and have a long service life. They are designed to be easy to access and repair, and they require minimal maintenance. Customizable - EOT Cranes can be customized to suit the specific needs of the application. They can be configured with different hoists, trolleys, bridges, and control systems to meet the specific needs of the application.
- All the motors of an EOT Crane are electric motors..
- It consists of a heavy-duty cast steel rope guide.
- It has an upper and lower hook travel limit switch.
- The girder is made up of welded steel.
- The body of the EOT cranes is corrosion resistance.
- It offers easy operation with minimum maintenance.
Single Girder EOT (Electric Overhead Traveling) Crane
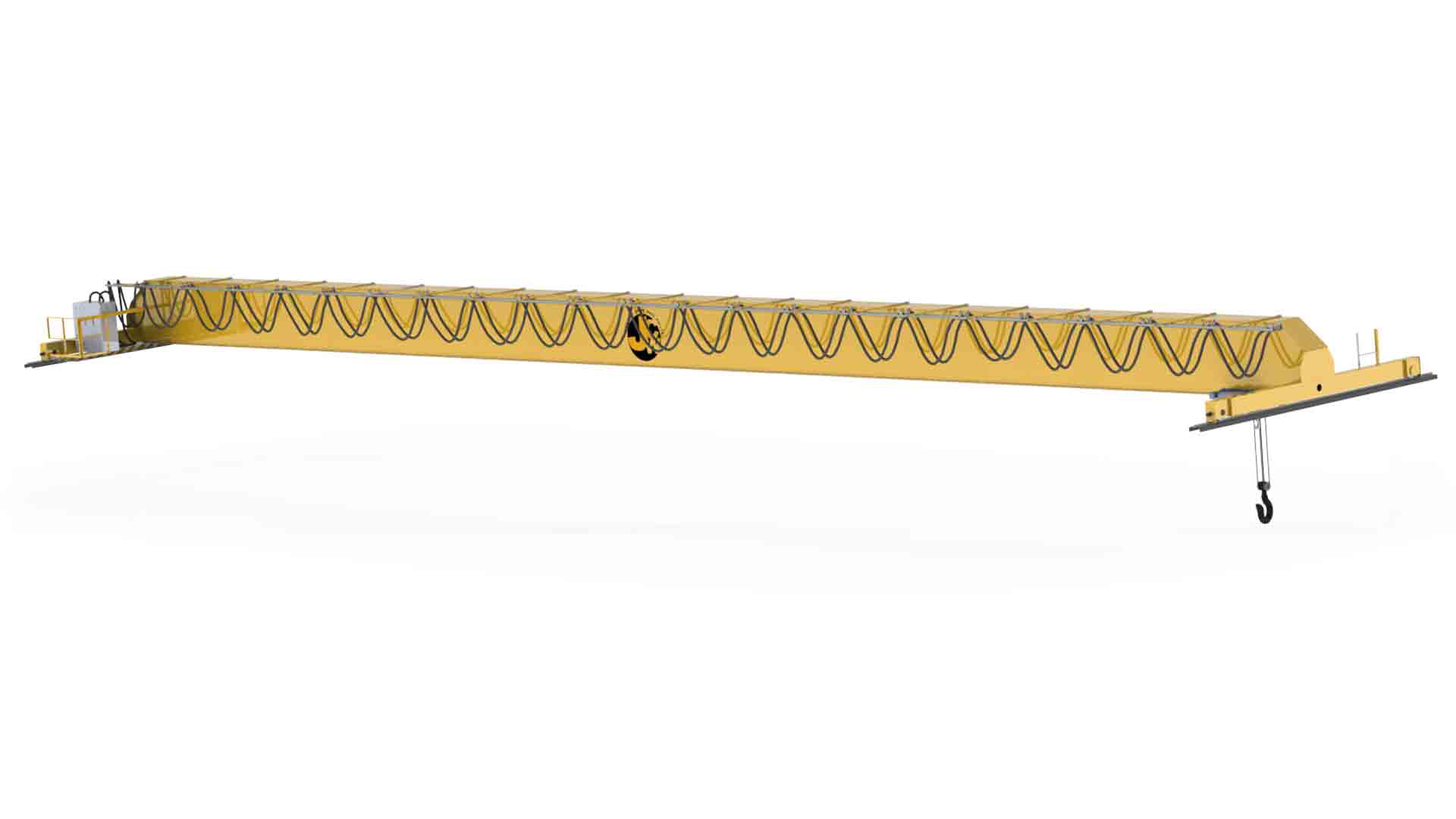
Single Girder EOT Crane has one main girder between the parallel runway. It consists of an electric hoist, which moves on the lower flange of the main girder. Single Girder EOT cranes do not need the rail component for moving on the parallel runway. Generally, single girder EOT cranes don’t have any platform. However, in some cases, it consists of 2 small platforms for LT (Long Travel) mechanism. It also consists of flanged mounted motors and vertical gearboxes. It can be operated through a push-button pendant station or radio remote control. However, these types of cranes cannot be operated by the cabin. The DC (Direct Current) Disc Brakes are used in all the movements of the cranes. The single girder cranes use a snap action limit switch, which is responsible for the movement of the hoist in an upward or downward direction. This switch is triggered by a wire rope guide. The single girder EOT crane is made up of 4-wheel arrangement in LT (Long Travel) end carriage. Because of this, the crane has a higher wheel load and also required heavy gantry girder, to improve the capacity. Single girder cranes are used in light applications such as handling normal material.
Features of Single Girder EOT Crane
- In Comparison to double girder EOT crane, single girder EOT cranes are much lighter, as it consists of one main bridge.
- It is suited for light industrial applications.
- It has compact construction which minimizes the building loads.
- It can lift up to 20 tons of loads.
- It reduces the total crane cost on crane components, runway structure and building.
- Low head rooms reduce the cost of shed/building
- Its ergonomic design offers manual long travel (LT) because of its electric hoist or motorized chain pulley block.
Double Girder EOT (Electric Overhead Traveling) Crane
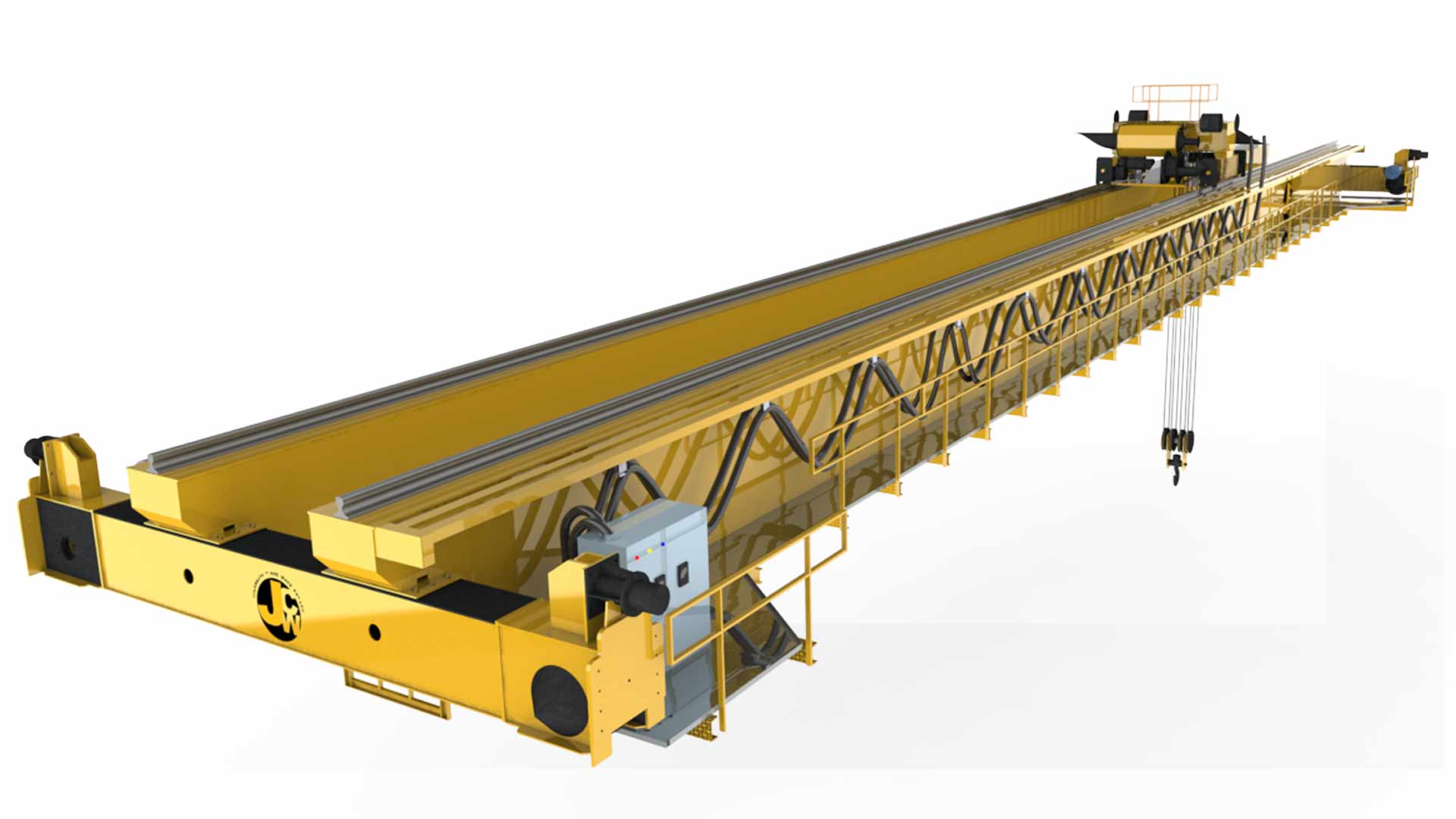
Double girder EOT crane has two main girders between the parallel runway. It has a crab mechanism that travels above both the girders, which run over the rails. The rails with platforms are used to maintain all the parts of the crabs. The double girder cranes have the platform on both sides. This is used for maintenance purposes and platforms for crab maintenance. It consists of foot mounted motors with horizontal gearboxes. It is operated by push-button pendant station, radio remote, or operating cabin mode. In double girder EOT crane, a rotary limit switch is used to calculate the hook traveling and the up and down movement should be controlled accordingly. An additional limit switch is used such as gravity limit switch. The gravity limit switch is used for securing the limit switch working. Double girder EOT cranes have an 8-wheel arrangement, so that wheel load will be less at a particular point. These types of cranes are easy to maintain.
Features of Double Girder EOT Crane
- As it consists of two main bridges, it becomes a sturdy and robust construction.
- It is specifically designed for assisting heavy-duty operations.
- It is cost-effective when compared to a single girder crane as it is capable of lifting heavy loads.
- It is utilized at any capacity, where a high hook lift is required. Because the hook can be pulled up between the girders.
- It has a lifting capacity of up to 250 tons.
- It consists of alloy steel, hardened, precision-cut gears.
- It consists of foot mounted hydraulic thruster brakes, which is used for the hoist.
- It has a full-length platform on the long travel drive of the side girder.
Applications of EOT Cranes are vast.They are used in Many Industries.
- Ceramic Industries - EOT cranes are a valuable asset in the ceramic industry, as they are able to efficiently and effectively handle the heavy raw materials, molds, and finished products that are present in the manufacturing process. These cranes can be customized to suit the specific needs of the application, ensuring that all materials are handled with precision and care.
- Power Plants - EOT cranes play a crucial role in power plants, where they are used to move heavy equipment, such as generators and turbines, during maintenance and repair. These cranes are able to handle large loads with ease and are equipped with safety features such as emergency stop buttons, limit switches, and overload protection to ensure the safety of the operator and the load.
- Transport Industry - EOT cranes are an essential piece of equipment in the transport industry, as they are used to efficiently load and unload cargo from trains, trucks and ships. They are able to handle large and heavy loads with ease and can be operated remotely, increasing productivity and efficiency.
- Petrochemical Industry - EOT cranes are an integral part of petrochemical plants, as they are used to move heavy equipment and chemicals during the production process. They are designed to withstand harsh environments and are able to handle large loads with precision and accuracy.
- Chemical Industries - EOT cranes play a vital role in chemical manufacturing, as they are used to move heavy raw materials, chemicals, and finished products.
- Steel Plant - EOT cranes are a crucial piece of equipment in steel production, as they are used to move heavy steel beams, slabs, and finished products. These cranes are able to handle large loads with ease and are equipped with safety features such as emergency stop buttons, limit switches, and overload protection to ensure the safety of the operator and the load.
- Dairy Industries - EOT cranes are an important asset in the dairy industry, as they are used to move heavy equipment, such as milking machines and storage tanks, as well as heavy raw materials and finished products. These cranes are easy to maintain and have a long service life, ensuring that they are available when needed.
- Foundries - EOT cranes are a vital piece of equipment in foundries, as they are used to move heavy raw materials, molds, and finished products. These cranes are able to handle large loads with ease and are equipped with safety features such as emergency stop buttons, limit switches, and overload protection to ensure the safety of the operator and the load.
- Textile Industry - EOT cranes are a valuable asset in the textile industry, as they are used to move heavy raw materials, such as cotton and wool, as well as finished products, such as fabrics and clothing. These cranes are easy to maintain and have a long service life, ensuring that they are available when needed.
- Cement Industry - EOT cranes play a vital role in the cement industry, as they are used to move heavy raw materials, such as limestone and clay, and finished products, such as cement. These cranes are able to handle large loads with ease and are equipped with safety features such as emergency stop buttons, limit switches, and overload protection to ensure the safety of the operator and the load.
- In Assembly Line - EOT cranes are an essential piece of equipment in assembly lines, as they are used to move heavy equipment and materials during the manufacturing process. These cranes are highly efficient and can be customized to suit the specific needs of the application, ensuring that all materials are handled with precision and care.
- Paper and Packing - EOT cranes are a valuable asset in the paper and packing industry, as they are used to move heavy raw materials, such as wood pulp, and finished products, such as paper rolls and cardboard boxes. These cranes are easy to maintain and have a long service life, ensuring that they are available when needed.
- Petro-Chemical - EOT cranes are used in the petrochemical industry to move heavy equipment and chemicals during the production process.
- Shipbuilding - EOT cranes are used in ports and terminals for loading and unloading cargo from ships and transporting it to warehouses and other storage facilities. They are also used in loading and unloading cargo from railway cars and trucks. These cranes are highly efficient and can handle large loads with ease, increasing productivity and efficiency in the logistics industry.
- Fertilizers - EOT cranes are an important piece of equipment in the fertilizer industry, as they are used to move heavy raw materials, such as phosphates and potash, and finished products, such as fertilizer bags. These cranes are able to handle large loads with ease and are equipped with safety features such as emergency stop buttons, limit switches, and overload protection to ensure the safety of the operator and the load.
- Renewable Energy - EOT cranes play a vital role in the renewable energy industry, as they are used in facilities such as wind and solar power plants to move heavy equipment and materials during the construction and maintenance process. These cranes are able to handle large loads with ease and are equipped with safety features such as emergency stop buttons, limit switches, and overload protection to ensure the safety of the operator and the load. Additionally, these cranes are also used to maintain and service wind turbines, ensuring smooth and efficient operation of the power plant.
- Recycling - EOT cranes are an essential piece of equipment in the recycling industry, as they are used to move heavy waste materials and finished products. These cranes are able to handle large loads with ease and are equipped with safety features such as emergency stop buttons, limit switches, and overload protection to ensure the safety of the operator and the load. They are also designed to operate in harsh and demanding environments, making them ideal for use in recycling facilities.
- Marine - EOT cranes are an important piece of equipment in marine operations, as they are used in oil rigs and ports to move heavy equipment and materials. These cranes are able to handle large loads with ease and are equipped with safety features such as emergency stop buttons, limit switches, and overload protection to ensure the safety of the operator and the load. Additionally, these cranes are also designed to operate in harsh and demanding marine environments, making them ideal for use in ports and oil rigs.
- Pulp and Paper - EOT cranes play a vital role in the pulp and paper industry, as they are used in mills to move heavy raw materials, such as wood pulp, and finished products, such as paper rolls. These cranes are able to handle large loads with ease and are equipped with safety features such as emergency stop buttons, limit switches, and overload protection to ensure the safety of the operator and the load. Additionally, these cranes are also designed to operate in harsh and demanding environments, making them ideal for use in pulp and paper mills.
- Waste Management - EOT cranes are an essential piece of equipment in the waste management industry, as they are used to move heavy waste materials and finished products. These cranes are able to handle large loads with ease and are equipped with safety features such as emergency stop buttons, limit switches, and overload protection to ensure the safety of the operator and the load. They are also designed to operate in harsh and demanding environments, making them ideal for use in waste management facilities.
- Agriculture - EOT cranes play a crucial role in the agriculture industry, as they are used to move heavy equipment, such as tractors and harvesters, and materials, such as hay bales and grain. These cranes are able to handle large loads with ease and are equipped with safety features such as emergency stop buttons, limit switches, and overload protection to ensure the safety of the operator and the load. Additionally, these cranes are also designed to operate in harsh and demanding environments, making them ideal for use in agriculture operations.
Malfunctions of EOT Cranes.
-
Damaged wires/ropes
- Many times , wire ropes are frayed, kinked or broken . Due to wear and tear wire rope diameter also reduces. This can put the lives of the workers at risk due to high probability of the falling of the product from the hook.
-
Electrical dangers or fault in power circuit
- Electricity is dangerous . Due to fault in wiring or control panel , high current can flow which can damage the motors ,VFDs & any other electrical equipment.
-
Hooks getting bent or damage
- Hooks getting bent or damaged can be a serious issue and it can be a risk for life . Workers must check for this for safety reasons before lifting any load. They should look for any damage such as cracks , bending or stretching.
-
4. Crane Skew or Alignment issues
- Crane Skew can give you a costly expense if it’s not looked properly. It will give different hints if there is an alignment issues such as thumping, grinding, loud scratching, If the power usage is more and even if crane is dragging or lulling in position.
-
5. Overheating
Overheating can occur in the crane's motors or other electrical components, leading to damage or failure. -
6. Load Balancing Issues
Improperly balanced loads can lead to damage or failure of the crane. -
7. Weather Damage
EOT Cranes are often used in outdoor environments and can suffer from weather-related damage, such as rust and corrosion from exposure to the elements.
Comparison of EOT Cranes with Other Types of Cranes
Electric Overhead Traveling (EOT) cranes are a popular type of crane used in various industries for moving heavy loads. However, they are not the only option available. In this article, we will compare EOT cranes to other types of cranes such as gantry cranes, jib cranes, and monorail cranes to help businesses make an informed decision when choosing the right crane for their specific needs.
-
Gantry Cranes
Gantry cranes are similar to EOT cranes in that they both consist of a bridge that spans the width of a bay and a trolley that runs along the bridge. However, gantry cranes are supported by legs rather than a building structure. This makes them more versatile, as they can be used both indoors and outdoors. Gantry cranes are also typically larger and can handle heavier loads than EOT cranes. On the other hand, EOT cranes have the advantage of being able to utilize the existing building structure for support, which can save on costs and increase the available headroom.
-
Monorail Cranes
Monorail cranes consist of a single beam that runs the length of the bay, with a trolley running along the beam. They are similar to EOT cranes in that they both have a bridge and trolley, but monorail cranes do not have the additional overhead structure of EOT cranes. This makes them more cost-effective and easier to install. However, monorail cranes are limited in their capacity and are typically used for lighter loads and shorter spans. EOT cranes, on the other hand, can handle heavier loads and longer spans, and can utilize the existing building structure for support.
Jib Cranes
Jib cranes are smaller than EOT cranes and are typically used for smaller loads and shorter spans. They consist of a horizontal boom that is mounted on a vertical mast and can rotate 360 degrees. Jib cranes are ideal for applications where space is limited and a small footprint is required. EOT cranes, on the other hand, are better suited for larger loads and longer spans, and can cover a wider area.
EOT cranes, gantry cranes, jib cranes, and monorail cranes all have their own unique advantages and disadvantages. Businesses should carefully consider their specific needs and requirements before choosing the right crane for their application. EOT cranes are ideal for heavy loads and long spans, and can utilize the existing building structure for support. Gantry cranes are versatile and can be used both indoors and outdoors, but are typically larger and more expensive. Jib cranes are ideal for small loads and short spans in limited space, while monorail cranes are cost-effective and easy to install but are limited in their capacity.
Conclusion
EOT cranes offer reliability, safety, and better speed. EOT cranes are used for wide applications such as Ceramic Industries, Power Plant, Cement Industry, etc. It can be used to lift light weights as well as heavy loads. EOT can reduce the man power required as compared with the Gantry, Monorail, Goliath, Jib cranes and also the cost gets reduced due to easy handling of EOT crane. EOT crane can be operated with Radio Remote controls which makes it less risky for the crane operator. EOT cranes have low maintenance equipment . Double Girder crane has the capacity to lift up to 250 tons and single girder crane has the capacity of 20 tons.
Anand Systems Engineering is an Indian manufacturer of Radio Remote Control systems for Cranes and Hoists with a Goal of modernizing Indian Engineering.
Follow us on YouTube.
Designing an EOT (Electric Overhead Traveling) Crane: An In-Depth Guide
Introduction
In the world of material handling, EOT cranes play a pivotal role in the efficient movement of heavy loads within an industrial environment. These cranes are commonly found in manufacturing plants, warehouses, and assembly lines where they transport large items over short distances. The design of an EOT crane is a complex task that requires a deep understanding of engineering principles, safety standards, and operational requirements. This article delves into the semi-technical aspects of designing an EOT crane, ensuring it is both informative and engaging for readers seeking to understand the intricacies involved in the creation of these powerful machines.
Understanding EOT Cranes
An EOT crane consists of three primary components: the bridge, the hoist, and the runway. The bridge spans the width of the workspace and moves along the runway, which is attached to the walls or columns of the facility. The hoist, which lifts and lowers the load, travels along the bridge. The entire system is powered electrically, hence the name Electric Overhead Traveling crane.
Design Considerations
Load Capacity:
The foremost consideration in designing an EOT crane is its load capacity, which is determined by the maximum weight the crane is expected to lift. This capacity influences the selection of materials, the dimensions of the crane components, and the power of the motors.
Span and Lifting Height:
The span, or the distance between the runways, and the lifting height, or the distance between the lowest and highest points the hoist can move, are critical dimensions that must be tailored to the facility’s layout and the operational needs.
Speed:
The crane’s speed, including the hoisting and traveling speed, affects the efficiency of operations. Designers must balance the need for speed with precision and safety.
Duty Cycle:
The duty cycle refers to the crane’s operational pattern. It includes the number of lifts per hour, the percentage of the crane’s capacity used per lift, and the average load lifted. This cycle impacts the durability and design of the crane.
Control System:
Modern EOT cranes are equipped with sophisticated control systems that allow for precise movements and enhanced safety features. Designers must choose between pendant controls, wireless remote controls, or cabin-operated controls based on the application.
Structural Design
The structural design of an EOT crane involves detailed calculations to ensure strength, stability, and safety. Engineers use finite element analysis (FEA) to simulate the crane’s performance under various load conditions and to optimize the design for weight and cost efficiency.
Bridge Design:
The bridge must be rigid enough to prevent excessive deflection or bending when carrying loads. It is typically made of structural steel and designed as a box girder or a truss.
End Carriages:
Located at either end of the bridge, the end carriages house the wheels that travel along the runway. Their design must account for the distribution of the load and the forces exerted during movement.
Hoist Design:
The hoist is the heart of the EOT crane. It comprises the motor, gearbox, drum, wire rope, and hook. The design of the hoist must ensure smooth operation, reliable braking, and adherence to safety standards.
Electrical Design
The electrical design is crucial for the safe and efficient operation of an EOT crane. It includes the selection of motors, drives, brakes, and other electrical components. The electrical system must be designed to handle the starting, running, and stopping of the crane without causing electrical overloads or mechanical stress.
Motor Selection:
Motors must be chosen based on the required speed, torque, and power. They should also be rated for the specific duty cycle of the crane.
Drive Systems: Variable frequency drives (VFDs) are often used to control the speed of the crane smoothly and to reduce mechanical stress during starting and stopping.
Safety Features:
Electrical safety features include limit switches, overload protection, and emergency stop functions. These features prevent accidents and equipment damage.
Material Selection
The materials used in the construction of an EOT crane must be both strong and durable. High-strength steel is commonly used for structural components, while wire ropes are made from high-carbon steel for flexibility and strength. The choice of materials affects the crane’s performance, longevity, and maintenance requirements.
Manufacturing and Assembly
Once the design is finalized, the manufacturing process begins. Precision fabrication techniques are employed to ensure that all components meet the specified tolerances. After fabrication, the components are assembled, either on-site or at the manufacturer’s facility, and the crane is rigorously tested to ensure it meets all design criteria and safety regulations.
Conclusion
The design of an EOT crane is a meticulous process that requires a synergy of mechanical, electrical, and structural engineering. By considering factors such as load capacity, speed, duty cycle, and control systems, engineers can create cranes that are not only functional but also safe and reliable. As technology advances, the design of EOT cranes will continue to evolve, incorporating new materials and control systems to meet the ever-changing demands of industry.
Manufacturing and Assembly of EOT Cranes
The manufacturing and assembly of EOT (Electric Overhead Traveling) cranes are critical stages that transform the conceptual designs into functional machinery. This process involves several intricate steps, each requiring precision and adherence to the highest standards of quality.
Let’s delve deeper into these stages:
Material Procurement and Quality Assurance
Before the actual manufacturing begins, it is essential to source high-quality materials that comply with industry standards. The procurement process involves selecting suppliers who can provide materials like structural steel, wire ropes, and electrical components that meet the specific requirements of the crane design.
Once the materials are procured, they undergo rigorous quality assurance tests. These tests ensure that the materials have the necessary mechanical properties, such as tensile strength and ductility, and are free from defects that could compromise the crane’s integrity.
Fabrication of Structural Components
The fabrication of the crane’s structural components is a meticulous process. It starts with cutting the steel to the precise dimensions specified in the design blueprints. Advanced machinery, such as CNC (Computer Numerical Control) plasma cutters, is often used for this purpose to achieve high accuracy.
After cutting, the steel sections are shaped and formed using processes like bending, rolling, and welding. The welding process, in particular, is crucial as it must be performed by certified welders to ensure strong and durable joints. Non-destructive testing methods, such as ultrasonic testing, are employed to inspect the welds and detect any internal flaws.
Assembly of Mechanical and Electrical Systems
The mechanical components, such as the hoist, trolley, and end carriages, are assembled separately. Each component is built to exact specifications, ensuring that they fit together seamlessly during the final assembly.
The electrical systems are equally important. The assembly involves wiring the motors, installing the control panels, and setting up the safety devices. Technicians must carefully follow the electrical schematics to ensure that all connections are secure and comply with electrical codes.
Painting and Finishing
Once the structural components are fabricated and the mechanical and electrical systems are assembled, the crane undergoes painting and finishing. This step not only enhances the crane’s appearance but also provides a protective layer against corrosion and wear.
The painting process typically involves surface preparation, such as sandblasting, to remove any rust or impurities. Then, a primer is applied, followed by one or more coats of paint. The choice of paint is critical, as it must withstand the harsh conditions of the industrial environment where the crane will operate.
Final Assembly and Testing
The final assembly of the EOT crane takes place either at the manufacturer’s facility or on-site, depending on the size and complexity of the crane. The structural components, mechanical systems, and electrical systems are brought together to form the complete crane.
After assembly, the crane undergoes a series of tests to verify its functionality and safety. These tests include load testing, where the crane is required to lift weights exceeding its rated capacity, and operational testing, where all movements and controls are checked for smooth and precise operation.
Quality Control and Certification
Throughout the manufacturing and assembly process, quality control is paramount. Inspectors ensure that each stage of production meets the predefined standards and that the final product is ready for certification.
The crane is subjected to a final inspection by a third-party certifying body, which assesses its compliance with international safety standards. Once certified, the crane is deemed safe for use and ready for delivery to the customer.
Conclusion
The manufacturing and assembly of an EOT crane are as much an art as they are a science. It requires a harmonious blend of skilled craftsmanship, precise engineering, and stringent quality control. By meticulously following each step, manufacturers can deliver EOT cranes that are robust, reliable, and ready to take on the challenges of any industrial setting.
Quality Control and Certification of EOT Cranes: Ensuring Safety and Reliability
EOT cranes form part of modern industrial settings, ensuring precision and efficiency in the movement of heavy loads. However, their safe operation relies on rigorous quality control and certification. In this article, we delve into the intricacies of ensuring the quality and reliability of EOT cranes, from manufacture to deployment.
Understanding Quality Control
Quality control is the series of systematic actions conducted to maintain consistent product quality. For EOT cranes, the process of quality control begins at the manufacturing stage and extends through the crane's lifecycle. Let's look deeper into the critical aspects of QC:
1. Material Inspection and Selection
Incoming Material Inspection: The first step is to inspect raw materials (such as structural steel, wire ropes, and electrical components) upon arrival. QC personnel verify that the materials meet specified standards, including mechanical properties, dimensions, and surface finish.
Traceability: Each material batch must be traceable to its source. This ensures that any defects or issues can be traced back to the supplier.
2. Fabrication and Welding Quality
Welding Procedures: Certified welders follow approved welding procedures to join structural components. QC inspectors verify weld quality, including penetration, fusion, and absence of defects.
Non-Destructive Testing (NDT): Techniques like ultrasonic testing and magnetic particle inspection detect hidden flaws in welds and other critical areas.
3. Assembly and Fitment Checks
Dimensional Accuracy: Components must fit precisely during assembly. QC personnel verify dimensions, clearances, and alignments.
Bolt Torque: Properly torqued bolts prevent loosening during operation. QC checks ensure consistent torque values.
4. Painting and Surface Treatment
Surface Preparation: Before painting, surfaces undergo sandblasting or chemical cleaning to remove rust, scale, and contaminants.
Paint Adhesion: QC assesses paint adhesion, thickness, and coverage. Properly coated surfaces resist corrosion.
5. Functional Testing
Load Testing: The EOT cranes carry out load testing to guarantee the lifting capacity of the cranes. The load is more than the rated capacity of the crane for safety margins.
Travel and Hoisting Tests: The smoothness of movements, braking, and emergency stop functions are checked by the QC.
6. Electrical and Control Systems
Electrical Connections: The inspectors carry out checking of proper wiring, grounding, and insulation. Functional tests are carried out on control panels.
Safety Devices: The limit switches, overload protection, and emergency stops get tested for reliability.
Certification and Compliance
Certification is necessary for making an EOT crane comply with all safety standards and regulatory requirements. The following are the primary certifications:
1. CE Marking
European Conformity (CE): EOT cranes sold in the European Union (EU) must carry the CE mark. It shows that a product has complied with EU safety directives.
2. IS Standards (Indian Standards)
IS 3177: It provides the specification for EOT cranes in design, fabrication, and testing.
IS 4137: It deals with the electrical aspects of the motor ratings, control systems, and safety features.
3. FEM Standards (European Materials Handling Federation)
FEM 9.755: It provides the guideline for crane design, manufacturing, and safety.
4. ASME B30 Standards (American Society of Mechanical Engineers)
B30.2: It deals with overhead and gantry cranes, including EOT cranes.
5. ISO 9001:2015
Quality Management System: A manufacturer with ISO 9001 certification implies a commitment to quality processes.
Quality control and certification are a must for EOT cranes. The manufacturer can be sure of the safety and reliability aspects of the operation of these powerful machines when he meets these stringent standards and ensures compliance. Lifting industries to new heights with safety!
The Journey of EOT Cranes: From Concept to Commissioning
In the bustling heart of industry, EOT cranes stand as silent heroes. These steel giants lift, shift, and place heavy loads with a grace that belies their immense power. But have you ever wondered about the journey these cranes undertake before becoming the backbone of warehouses and assembly lines? Let’s delve into the intricate supply chain of EOT cranes—from the initial concept to their final installation on the factory floor.
1. Design and Engineering: The Blueprint of Strength
It all begins with an idea—a need for a machine capable of handling the heaviest lifting. Engineers and designers collaborate, sketching out blueprints that will eventually transform into an EOT crane. They calculate, model, and simulate, ensuring that every beam, bolt, and cable can withstand the tremendous loads it will bear. This stage sets the foundation for the crane’s future performance, determining its capacity, span, lifting height, and speed.
2. Sourcing Materials: The Quest for Quality
With designs in hand, the procurement team embarks on a quest for top-quality materials. Steel for strength, wire ropes for durability, and electrical components for reliability—all carefully vetted. Each component becomes a vital link in the crane’s chain, leaving no room for weak points.
3. Fabrication: Where Metal Takes Shape
In the skilled hands of craftsmen, raw materials transform. Steel beams are cut, shaped, and meticulously welded into the crane’s skeleton. Precision is paramount, and advanced technology, like CNC machinery, ensures every angle is accurate. This stage is a symphony of sparks and steel—an ode to human ingenuity.
4. Assembly: Piecing Together Power
Component by component, the EOT crane comes alive. The hoist and trolley—mechanical systems—are painstakingly assembled. Electrical systems are carefully wired, promising the thrill of movement. Every nut, bolt, and cable contributes to the crane’s portrait, painted with the brush of precision.
5. Painting and Finishing: The Final Touches
Before the crane flexes its muscles, it needs armor. Painting and finishing provide more than just aesthetics; they shield the crane from corrosion and wear. Layers of paint ensure it can withstand the harsh industrial environment. It’s the crane’s coat of arms, applied with pride.
6. Testing and Quality Assurance: Trial by Fire
No crane leaves the assembly line without proving its mettle. Load tests push it beyond its limits, travel tests ensure smooth operation, and safety systems undergo rigorous checks. It’s a trial by fire, and only those that pass earn the mantle of an EOT crane.
7. Shipping and Installation: The Voyage to Valor
After testing, the crane embarks on its journey to a new home. Whether by road, sea, or air, the destination remains the same: a place where it will lift, lower, and carry. Installation is the final step, where the crane is erected, commissioned, and entrusted to those who will command it.
8. After-Sales Support: A Lifelong Bond
The journey doesn’t end with installation. After-sales support ensures the crane continues to perform at its best. Maintenance, repairs, and upgrades—all part of the package, forging a lifelong bond between the crane and its makers.
An EOT crane’s supply chain is a saga of strength, precision, and reliability. It transforms raw materials into machines that drive progress. Behind every crane stands a team of people who design, build, and support these engineering marvels. So, the next time you see an EOT crane, remember the journey it took to get there and the people who made it possible.