C Track Systems vs. Conventional Cable Management: A Comparative Analysis
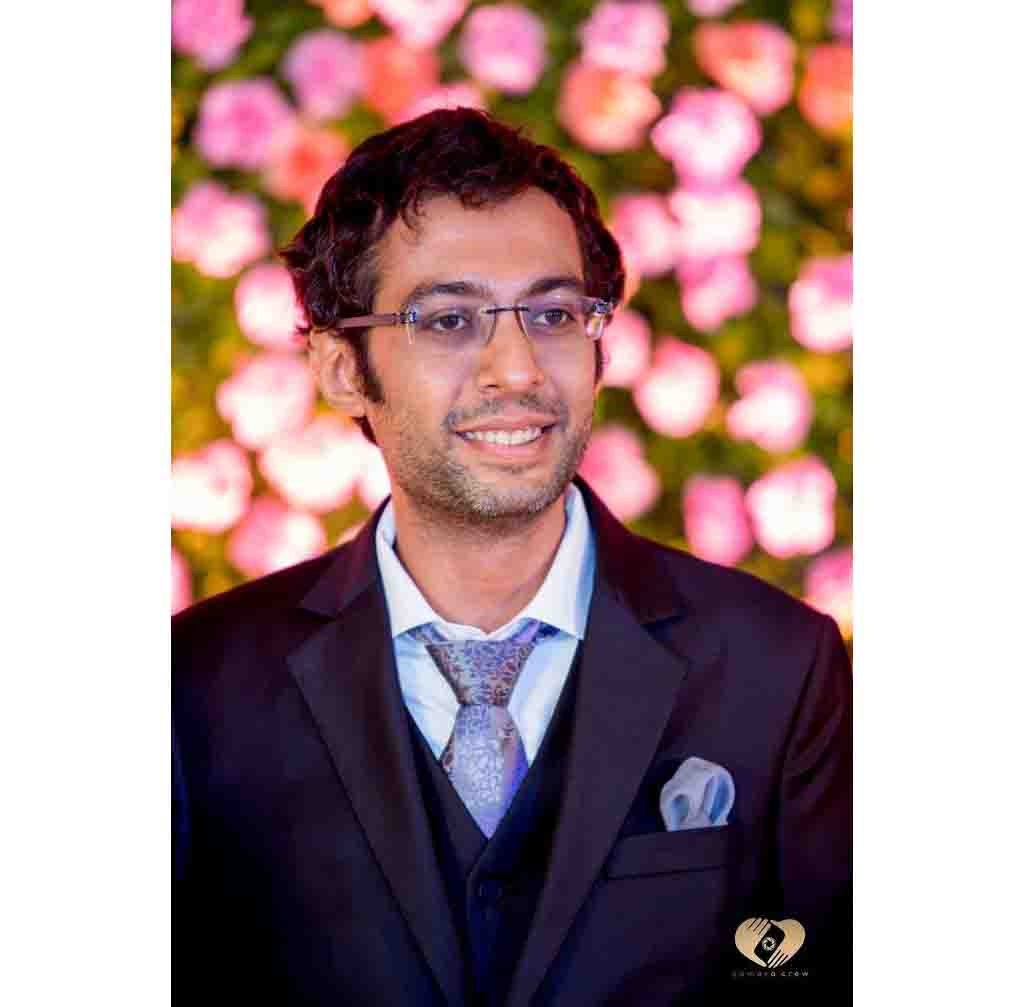
Anand Cable Fstooning system Accesories
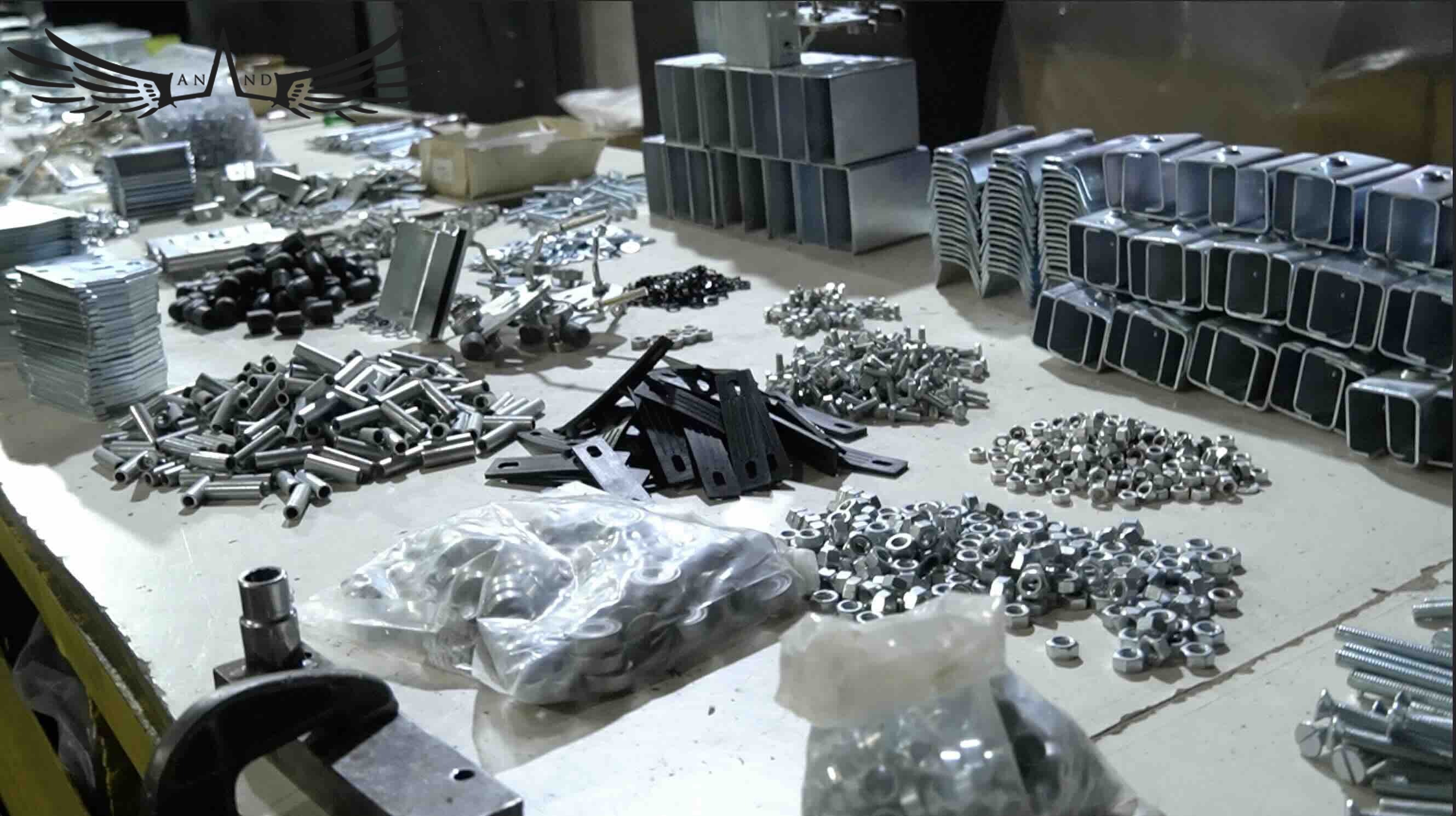
Anand C Track Accesories Manufacturing

In the realm of industrial cable management,choosing between C Track Systems and conventional methods can significantly impact the efficiency and safety of operations. This comparative analysis delves into the differences between the two, shedding light on the advantages and disadvantages to help businesses make informed decisions.
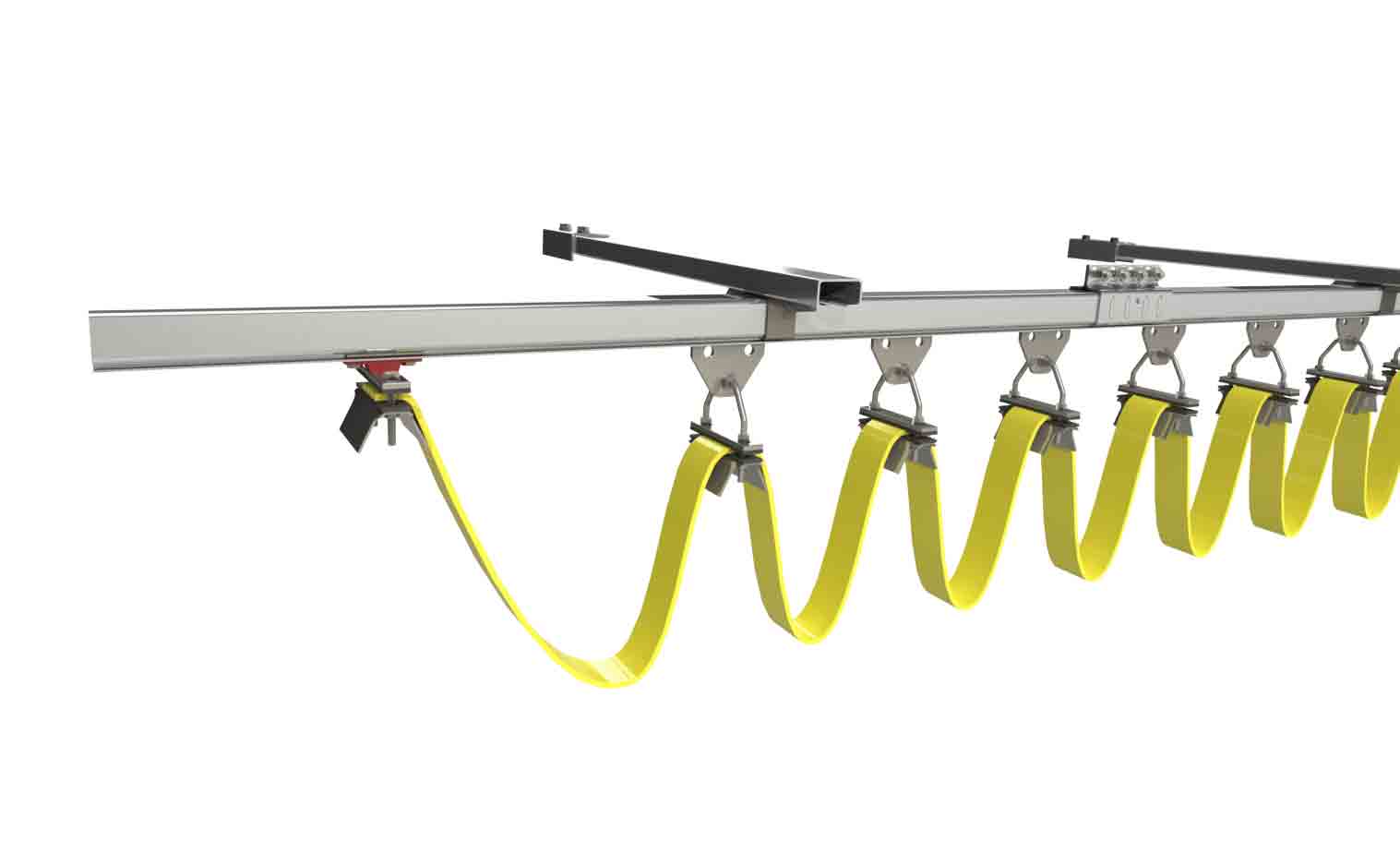
Understanding C Track Systems
C Track Systems are a modern solution to the age-old challenge of managing cables in industrial environments. These systems consist of a track structure with movable carriers that secure and guide cables along a predefined path. One of the key benefits of C Track Systems is their ability to accommodate a variety of cable types, including power cables, data cables, and pneumatic hoses, ensuring a streamlined and organized setup.
Anand Cable Festooning System
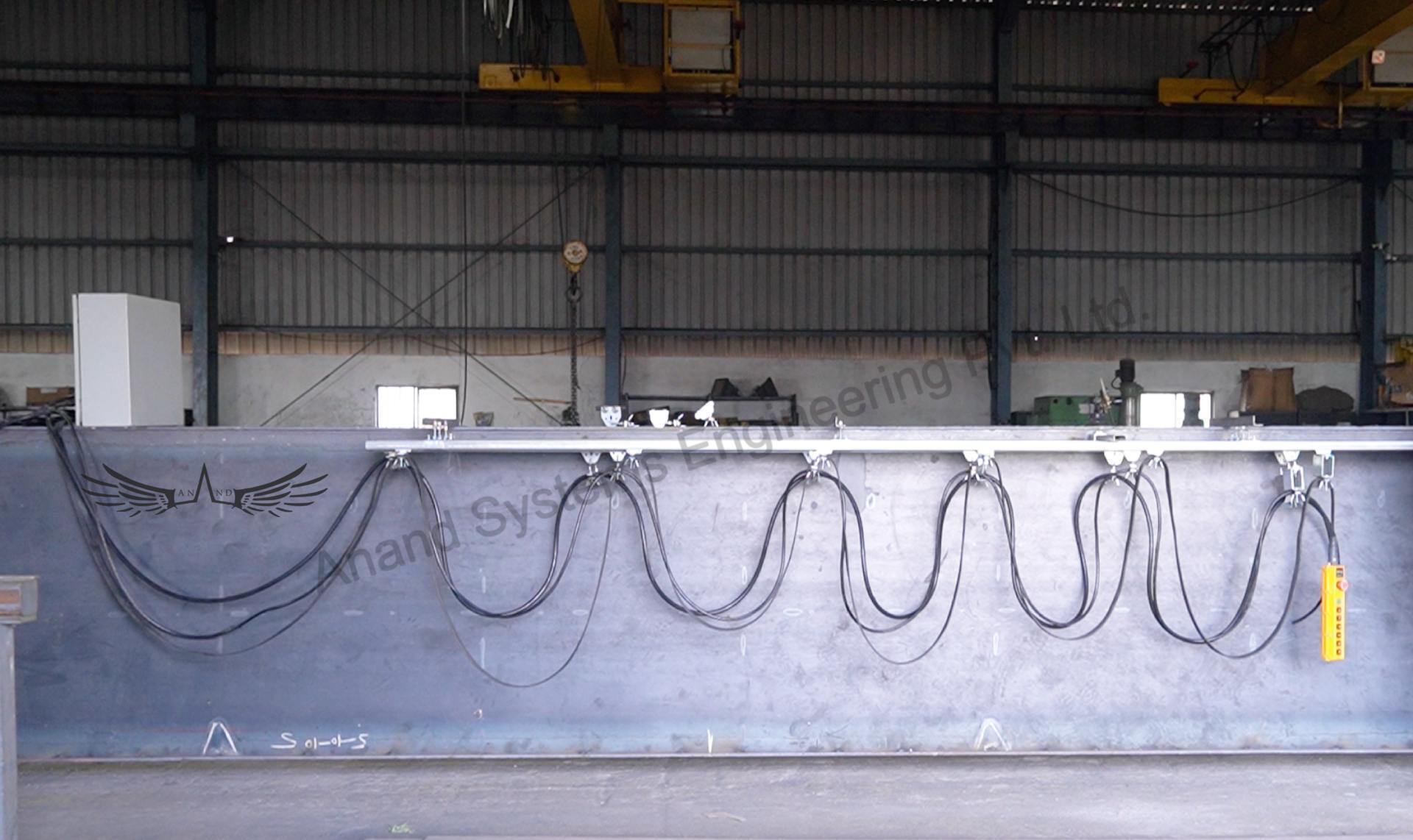
Conventional Cable Management
Conventional methods often involve cables suspended from hooks, laid on trays, or bundled together. While these methods are familiar, they come with limitations. Cables can become tangled, damaged, or pose tripping hazards, leading to operational disruptions and safety risks
Anand C Rail Hanger Clamp
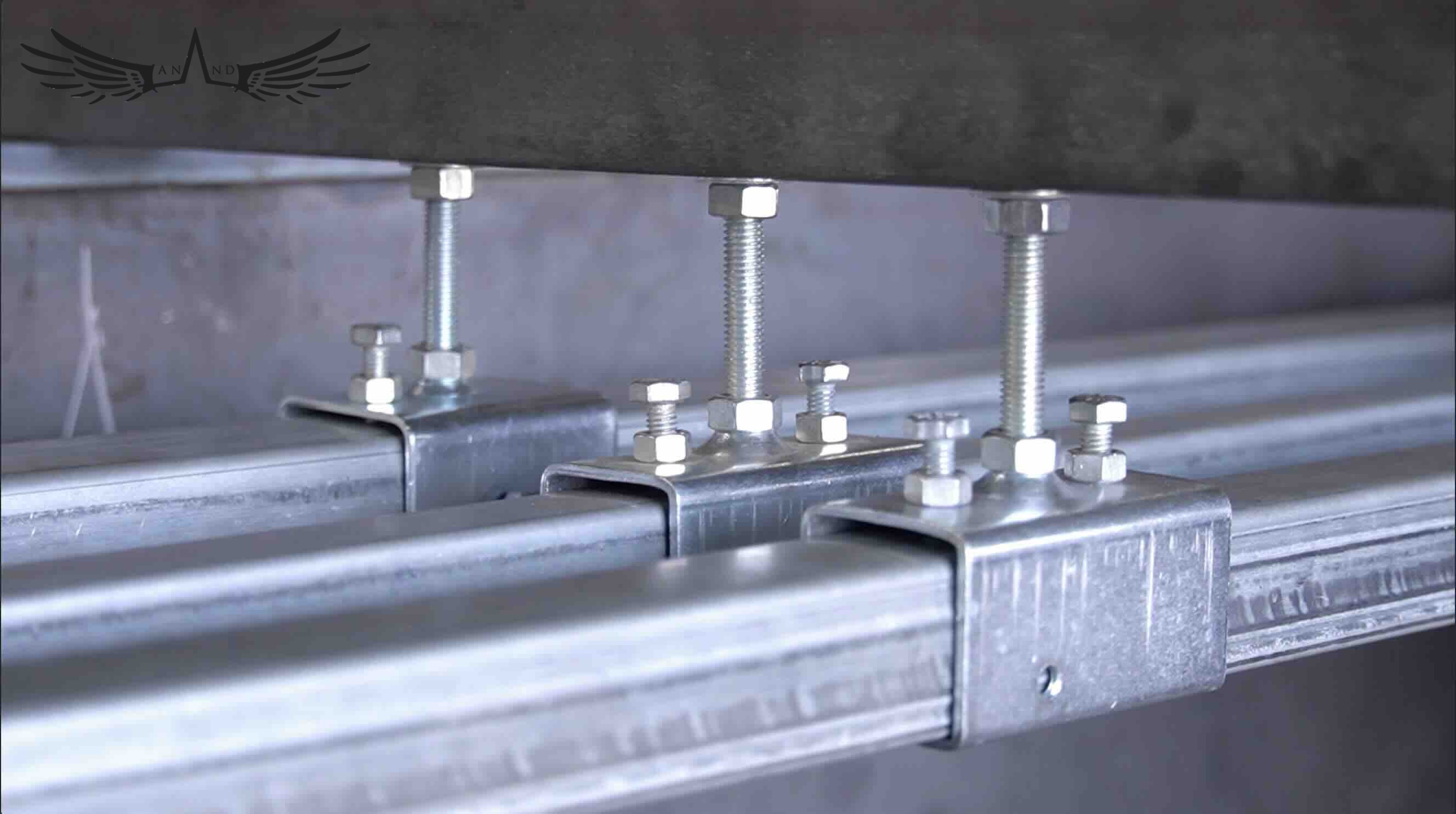
Comparative Analysis:
1. Space Efficiency
C Track Systems: Compact and customizable, they optimize space utilization, especially in areas with limited overhead clearance.
Conventional Cable Management: Requires more space due to the need for additional clearance for hanging or laying cables.
2. Flexibility
C Track Systems: Highly flexible, allowing easy modification and expansion without major disruptions to existing setups.
Conventional Cable Management: Less flexible and may require significant rework for modifications, leading to downtime.
3. Safety
C Track Systems: Enclosed tracks protect cables from external elements and prevent accidental contact, reducing the risk of electrical faults and injuries.
Conventional Cable Management: Exposed cables are prone to damage, posing a safety hazard to both equipment and personnel.
4. Maintenance
C Track Systems: Easier access for inspection and maintenance, leading to quicker issue resolution and reduced downtime.
Conventional Cable Management: Difficulties in locating and accessing specific cables can prolong maintenance processes.
FAQs (Frequently Asked Questions)
Q1: Can C Track Systems be customized for specific cable types?
A1: Yes, C Track Systems are highly adaptable and can be tailored to accommodate various cable types and sizes, ensuring a seamless
fit for different industrial applications.
Q2: Are C Track Systems suitable for outdoor use?
A2: Yes, there are weather-resistant C Track Systems designed specifically for outdoor applications, offering durability
and protection against harsh environmental conditions.
Q3: Can conventional cable management methods be retrofitted with C Track Systems?
A3: Yes, existing setups can often be retrofitted with C Track Systems, providing an efficient way to upgrade cable management infrastructure without extensive overhauls.
Q4: Which option is more cost-effective in the long run?
A4: While the initial investment for C Track Systems might be higher, their long-term benefits in terms of reduced maintenance costs, enhanced safety,
and operational efficiency often make them a more cost-effective choice over time.
Conclusion
In conclusion, while both C Track Systems and conventional cable management methods have their merits, the superior flexibility, safety, and efficiency of C Track Systems make them a compelling choice for businesses seeking to optimize their industrial cable management strategies. Making the right choice can lead to smoother operations, increased productivity, and a safer work environment